What is Extrusion Coating?
What is Extrusion Coating?
Extrusion coating is a process used to coat materials with a thin plastic layer using heat and pressure. This process is used to improve the durability and surface quality of paper, fabrics, aluminum foil and other plastic products. The coating is applied by pressure injecting molten plastic into a slot die that extrudes a thin membrane of plastic onto a moving sheet of recipient material. The combination is then cooled and compressed to form the end product. Depending on specific job requirements, extrusion coating can be used to coat both sides of the product or even produce laminates.
Plastic-coated products manufactured using extrusion coating techniques are found in a large number of day-to-day applications. These include coated board and paper products, coated woven fabrics used for fertilizer bags and a host of chemical, food and pharmaceutical packaging materials. These plastic coatings may be used for purely aesthetic purposes, to increase durability and quality of surface finishes and to produce aseptic packaging materials for sensitive or perishable products.
The extrusion coating process consists of a granular plastic heating and pressurization system similar to that used in injection molding. This feeds a constant stream of pressurized, molten plastic to an extruder head equipped with a narrow aperture slot die. The die extrudes a thin film of plastic over the substrate or recipient material as it is pulled off a roll. The coated substrate then passes between a pressure roller and water cooled chiller roller. These two rollers ensure the plastic coating is the correct thickness and is cooled to solidify and adhere to the substrate correctly.
The plastics used for extrusion coating are thermoplastic resins, such as polyethylene, polypropylene and ethylene vinyl acetate. They lend the substrates they are used to coat a wide variety of beneficial characteristics, greatly extending the scope of their use. These include moisture resistance, a hygienic contact barrier for products, reduced loss of product mass and heat sealing potential. Extrusion coating holds several advantages over other processes, including easy double-sided coating, high line speeds, solvent- and adhesive-free coating and variable coating thicknesses.
Extruded coating processes are flexible and allow for a range of user-defined finishes and coating structures. Substrates may be coated on both sides with ease and laminates consisting of alternating layers of different substrate materials and plastic are possible. Cooling roller surfaces can also be adapted or embossed to lend the coating a matte, gloss or decorative finish.
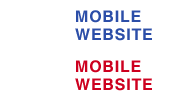
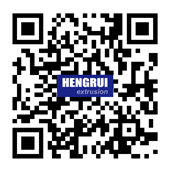