What is Plastic Extrusion?
What is Plastic Extrusion?
Plastic extrusion is a manufacturing process through which plastic is melted, shaped into a continuous profile, and cut to length. This process is used in the production of a wide variety of items, including piping, wire insulation, and plastic sheeting. Even adhesive tape and window frames include extrusion as part of their manufacturing processes.
In this process, raw plastic is fed into a heated extruder cavity or cylinder. Typically, the raw plastic is in bead form and may be mixed with colorants before the extrusion process begins, and in some methods, ultraviolet (UV) inhibitors may be added to the raw plastic beads as well. Once inside the machine, the plastic beads and any accompanying material move through an opening in the extruder cavity towards a screw mechanism. The screw rotates, forcing the plastic material to advance through the cavity.
Inside the cavity, the temperature is very high, often reaching about 400°F (200°C), which melts the plastic. Many exturders involve the use of three different heaters set to gradually increase heat inside the cavity. This reduces the potential for overheating.
Friction and pressure within the cavity serve to produce extra heat that is independent of the heaters. Sometimes, the pressure and friction inside the cavity produces so much heat that the heaters may be shut off. When this happens, the desired temperature is maintained by the friction and pressure. Cooling fans are also employed frequently, helping to keep the machine at the desired temperature.
When the molten plastic reaches the front of the barrel, it moves away from the screw and journeys through a special screen designed to filter contaminants out. The molten plastic then moves into a die, which is responsible for giving the molten plastic its profile. The plastic must then be cooled, often by a sealed-water bath; care must be taken to prevent the collapse of the newly formed product in its still molten state. Plastic sheeting and certain other products are cooled by special cooling rolls instead of water baths.
After cooling, the product is spooled, coiled, or cut to length. In addition to plastics, a variety of other materials, including aluminum and rubber, may be extruded. Even clay and certain types of foods may be produced this way. The process used may differ from that employed for the purpose of plastic extrusion, however.
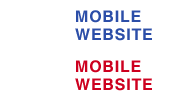
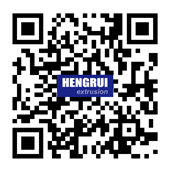