What's the Basic Process Of Plastic Extrusion
The plastic extrusion process begins with the placement of raw resin into the extruder’s hopper. If the resin lacks additives necessary for the particular application (such as UV inhibitors, anti-oxidants, or colorants), then they are then added to the hopper. Once in place, the resin is typically gravity-fed through the feed throat of the hopper down into the extruder's barrel. Within the barrel is a long, rotating screw that feeds the resin forward in the barrel towards the die.
As the resin moves along within the barrel, it is subjected to extremely high temperatures until it starts to melt. Depending on the type of thermoplastic, barrel temperatures can range between 400 and 530 degrees Fahrenheit. Most extruder's have a barrel that gradually increases in heat from the loading end to the feed pipe to enable gradual melting and minimize the possibility of plastic degradation.
Once the molten plastic reaches the end of the barrel, it is forced through a screen pack and fed into the feed pipe that leads to the die. The screen, reinforced by a breaker plate due to high pressures in the barrel, serves to remove contaminants that may be present in the molten plastic. The porosity of the screen, number of screens, and other factors can be manipulated until uniform melting occurs as a result of the right amount of back pressure.
Once in the feed pipe, the molten metal is fed into the die cavity, where it cools and hardens. To expedite the cooling process, the newly formed plastic receives a sealed water bath. In the case of plastic sheeting extrusions, cooling rolls replace the water bath.
Subscribe now
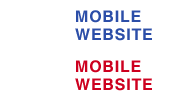
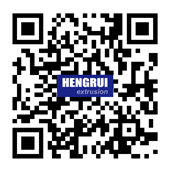